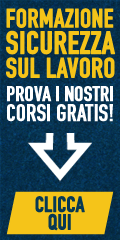
ROMA – Pubblicato dalla Commissione consultiva permanente per la salute e sicurezza sul lavoro un elenco di quattro nuove buone prassi validate il 23 gennaio 2013.
I quattro nuovi casi validati riguardano i seguenti aspetti:
- “Modulo risoluzione del rischio;
- Gestione del traffico nel magazzino;
- Valutazione dei rischi per attività di witness svolte presso terzi;
- Ribaltatore Bobine”.
“Modulo risoluzione del rischio”. La prima pratica validata e segnalata dalla Commissione riguarda la gestione dinamica e condivisa della valutazione e della risoluzione del rischio. “Ha lo scopo di formalizzare il flusso delle informazioni e segnalazioni che riguardano aspetti di sicurezza/ambiente all’interno dello stabilimento mettendo in atto un processo dinamico e partecipativo di valutazione e risoluzione del rischio in un ottica di coinvolgimento e consultazione di tutti i dipendenti”.
Chiave operativa è nell’uso di un modulo “Risoluzione del rischio” che tutti gli operatori hanno avuto e hanno l’obbligo di utilizzare per segnalare anomalie e rischi alla sicurezza riscontrati nel corso dei processi lavorativi.
“Il modulo di risoluzione del rischio è entrato in uso alla fine del 2007, da quella data ad oggi si è avuto un calo significativo nel numero di infortuni. Nel 2008 sono stati compilati direttamente dagli operatori di produzione\manutenzione ben 63 moduli di risoluzione del rischio che hanno riguardato azioni correttive di tipo sia tecnico che organizzativo”.
“Gestione del traffico nel magazzino”. Il secondo caso riguarda la logisitica e la gestione del traffico in un magazzino. L’azienda in questione ha introdotto un sistema volto a ridurre “rischi delle attività svolte in magazzino” causati dalla “contemporaneità di accessi e presenze”. “Il richio esistente era dovuto a possibili collisioni carrello – carrello e un rischio di schiacciamento carrello – uomo”.
Dopo i necessari brief tra Servizio di Prevenzione e Protezione, RLs e personale si è deciso di introdurre un sistema preventivo basato su quattro Azioni:
- AZIONE 1 – inserimento di specchi parabolici presso gli incroci e le postazioni di carico;
- AZIONE 2 – dotazione di tutti i carrelli di apposite luci blu;
- AZIONE 3 – implementazione di un sistema a semafori;
- AZIONE 4 – creazione di postazioni per gli autisti.
“L’insieme di queste azioni ha decisamente ridotto il rischio di incidenti in magazzino e migliorato le condizioni di lavoro e concentrazione dei carrellisti sulle modalità di stoccaggio, prelievo e carico avendo minori distrazioni dall’ambiente circostante.
Inoltre la migliore visuale permette una postura corretta e una diminuzione notevole di problemi”.
“Valutazione dei rischi per attività di witness svolte presso terzi”. Il terzo esempio è stato presentato da un’azienda che si occupa di certificazione di sicurezza di prodotti per il mercato europeo e nordamericano. La prassi ideata riguarda in particolare le certificazioni che i propri dipendenti effettuano direttamente nei laboratori dei clienti.
Tale attività chiamata witness ha evidenziato i seguenti rischi: gli operatori “non operano direttamente sui macchinari in test durante l’effettuazione della prova, ma possono aiutare gli operatori del cliente nelle fasi di set-up (con i conseguenti rischi meccanici derivanti dallo smontaggio dei macchinari) e comunque sono esposti ai rischi diretti che la prova comporta (come ad esempio elettrocuzione, esplosione ), soprattutto nel
caso non dovesse andare a buon fine. In più, è stata rilevata la criticità rappresentata dal livello di sicurezza degli ambienti di lavoro presso il cliente e dei rischi da interferenza dovuti alla presenza di altre attività nei locali dove gli addetti UL stazionano”.
Si è deciso quindi di introdurre una metodologia mirata e utile a valutare i rischi dell’attività di witness basata su questionari. Metodologia che ha porato a:
- “Raccogliere preventivamente informazioni sensibili già durante la fase di sopralluogo commerciale;
- migliorare la dotazione di DPI del personale;
- migliorare le modalità operative del personale presso i clienti;
- migliorare i vincoli contrattuali con il cliente al fine dei garantire un livello di sicurezza adeguato ai tecnici UL;
- formulare richieste verso i propri clienti in merito alla tipologia di ambienti, macchinari e personale da fornire per lo svolgimento delle attività di verifica”.
E ancora:
- “un miglioramento del clima aziendale;
- incrementare, grazie al loro coinvolgimento, la sensibilità dei lavoratori nei confronti delle tematiche di sicurezza sul lavoro, focalizzandone l’attenzione anche sulla propria sicurezza”.
“Ribaltatore Bobine”. Infine la quarta buona pratica segnalata dalla Commissione è stata ideata da un’azienda che si occupa di produzione industriale di imballaggio in materie plastice.
La criticità da affrontare era inerente la riduzione dei compiti di movimentazione manuale dei carichi nel reparto Coestrusione Film a Bolle. Ovvero del rischio di sovraccarico degli arti superiori al quale potevano essere esposti gli addetti all’accatastamento manuale di bobine in pile da 3.
Questa la soluzione: “installata nel reparto Coestrusione Bolle un’attrezzatura motorizzata (Ribaltatore Bobine o Tilt Table) in grado di ribaltare le bobine che vengono scaricate dal bobinatore della linea Coex”.
Risultati:
- riduzione al minimo dei compiti di movimentazione manuale per l’operatore;
- coinvolgimento operatori nella valutazione del rischio;
- abbattimento di denunce per malattia professionale e lamentele.
Info: buone prassi Commissione Consultiva Permanente.
Leggi anche: buone prassi validate 12 settembre.